How one manufacturing company is reaping rewards from its degree apprenticeship programme
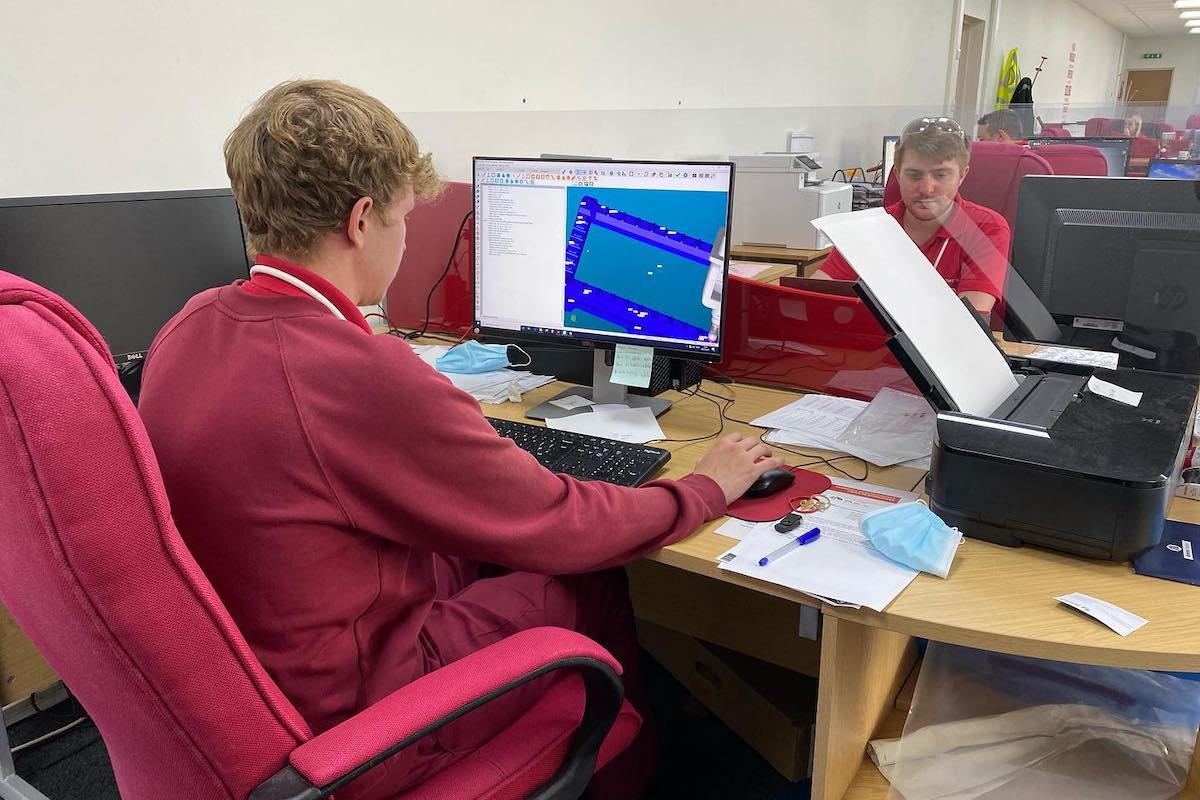
A degree level apprentice at Geometric Manufacturing learning the skills of a programmer
Manufacturing in the UK has been suffering from a crippling skills shortage for some years now. We asked Geometric Manufacturing managing director and Be the Business ambassador Paul Wenham to share his experience on plugging the skills gap at his business through a new degree apprenticeship programme.
"The skills shortage has hit the manufacturing industry hard and precision engineering hasn’t been an exception. As the MD of Geometric Manufacturing, CNC (computerised numerical control) machining specialists based in Tewkesbury, I can honestly say this skills shortage used to consume my thoughts as it was one of the main factors holding back growth in the business.
"For many years, we failed to recruit and train younger members of staff. The period after the financial crash was tough for engineering and we had our work cut out just to keep our existing staff fully occupied. But this was a foolhardy state of affairs to allow to creep into the business, because as those existing staff members started to retire, we suddenly became aware that we could no longer meet customer demands, and we had to work quickly to rectify this.
"By 2018, myself and the senior team realised that we needed to take action to address the shortfall of suitably skilled staff, but we soon found that the labour market couldn’t supply the talent necessary and there was fierce competition for any talent that did exist.
"Not only were the long-serving and skilled staff coming to the end of their working lives, but we were also having to embrace new technology in our factory. The latest CNC machines allowed us to tackle more complex work and operate in much more productive ways: we could be cost effective, offer fast lead times and the quality of our products improved. Although these new machines provided lots of benefits, they also brought challenges: setting, operating and especially programming this new machinery needed smart thinkers who could quickly pick up the technology and make it work effectively."
Tried and tested approach
"Apprenticeships have been the cornerstone of engineering for decades, and most of Geometric’s older staff had come through formal apprentice schemes in their early careers. So, when we were trying to solve these challenges, going back to first principles seemed like the logical approach. I started researching how our company could provide a degree level apprenticeship and found an academic partner in Wolverhampton University. We then started sending teams to attend local career days and exhibited some products.
"Our first degree apprentice started in September 2018, and we soon created a training programme which gives the apprentices rotations through each major manufacturing function in the business. The first 12 months are spent learning the processes from the ground up, operating the company’s CNC machine tools, and being trained in setting them. They are shown basic inspection techniques using measuring equipment and become fully conversant with safe operating procedures and good housekeeping, which are the core components of any manufacturing plant.
"In their second year, apprentices take on a six-month placement inside the production engineering department, where they learn how to plan and programme the manufacturing of parts produced. This includes external training delivered by the company’s CAM software vendor, and an accredited certificate of attainment.
"Their next six-month placement is spent in the quality department, where again they benefit from external training in the use and programming of the CNC Coordinate Measuring Machine and other inspection equipment. In their third year, time is spent setting machine tools, taking part in general projects. The skills acquired are brought into play in troubleshooting and assisting other staff and apprentices coming up through the programme behind them."
University connection
"Geometric’s first graduate has recently started a new role at the business as a continuous improvement engineer and is able to apply the learning from his studies to the workplace that he already understands so well. They are rewarded every six months with five per cent pay increments. By the end of their third year, they are already earning a salary of over £21,000 and have no student debt.
"Geometric’s first graduate has recently started a new role at the business as a continuous improvement engineer and is able to apply the learning from his studies to the workplace that he already understands so well.
"With ever increasing technical challenges in the modern factory, and new equipment such as robotics, 3D printing and laser cutting, having this pipeline of talent has never been more vital. We plan to add at least two new starters to the programme every year.
"Appropriately for National Apprentice Week, on 8 February 2022, Geometric has its first commercial degree apprentice commence her studies at Middlesex University on a B2B sales degree apprenticeship programme. This is an exciting moment for us and takes our current apprentice count to ten. Perhaps surprisingly for a manufacturing business, the gender balance of these ten is perfectly split, with five women forming part of the undergraduate cohort.
"To any business leaders wondering whether to bring apprentices into their business – I would say do it. Not only will you have a role to play in supporting and encouraging the talent of tomorrow, but you will also be creating sustainable growth for your business. The skills and talent shortage means that we all must work harder to create supportive work environments that encourage staff to stay and grow alongside the company. Apprenticeships are a fantastic way to do this."
-
location: South West (England)
-
business type: Manufacturing
-
business size: 10-49